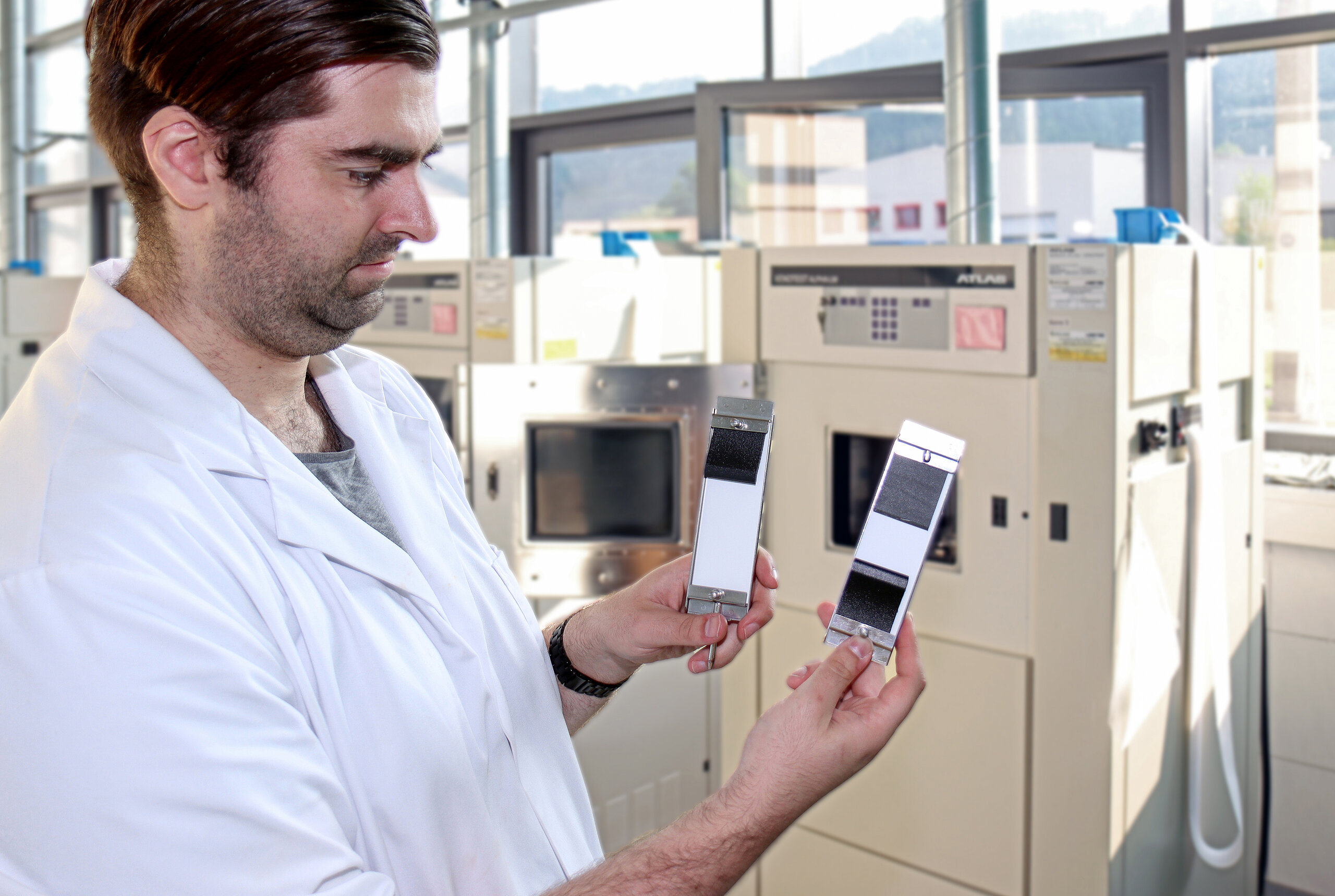
Laboratory technician Peter Fritzsche loads a xenon tester with sample carriers for exposure tests. (Photo: OMPG / Steffen Beikirch)
The subsidiary of the Thuringian Institute for Textile and Plastics Research (TITK) has had sun simulation and weathering tests in its portfolio since it was founded in 1992. Demand has risen sharply over the years. Manufacturers of every conceivable product want to ensure that their products outperform the competition in terms of durability and resistance. They should not become brittle or cracked, nor should they fade or yellow. Above all, however, they should reliably retain their function.
Possible weak points are detected by OMPG by means of an accelerated weathering test. In the past, the materials had to be stored outdoors for a long time, but now they undergo an artificial ageing process in the laboratory, virtually in fast motion. The testing company puts both material samples and complete end products under the microscope. On request, it can also produce test specimens itself from customer granulates. The samples are then exposed to precisely defined weathering factors in accordance with various standards.
One example is artificial exposure or weathering in accordance with DIN EN ISO 4892-2, where plastics of all kinds are tested for their suitability for indoor or outdoor use. This is done using a xenon test device that can simulate the effects of natural light outdoors or behind window glass using various filters. This is done in combination with the factors of temperature and humidity, and even rain if required. The interaction of these influences with UV radiation can seriously change the properties of materials.
Second example: textiles are stored in artificial light at a surface temperature of around 100 degrees Celsius (also known as the black standard temperature) in order to test their color fastness and ageing resistance. This temperature can certainly be reached in a car parked in the summer sun. The relevant standard is DIN EN ISO 105-B06 with the long name “Color fastness and aging to artificial light at high temperatures”. “The materials generally have to endure several cycles. This can take anywhere from a few days to five weeks,” says Deputy Laboratory Manager Monika Nicolai.
With a total of five xenon devices and two sunlight simulation chambers, OMPG currently serves many customers in Germany and abroad. One reason for the ever-increasing demand, particularly from the automotive industry, is the ever-shorter development cycles for new vehicle models. Lead times are decreasing, which means that suppliers have to be fast and flexible if they want to bring new and, above all, safe products onto the market.
In addition to sun simulation and weathering tests, clients often make use of other competencies of the accredited testing service provider OMPG. For example, tests on abrasion and soiling behavior, scratch resistance or the saliva, sweat and wash fastness of textiles and toys are requested. And with the scientific expertise of the TITK research institute and almost 30 years of experience behind it, possible shortcomings in the composition of the tested materials can not only be quickly identified, but also reliably rectified if necessary.
Technology used:
Xenotest Alpha+ and Xenotest 440 (Atlas MTT GmbH) can be used to test the lightfastness and weathering stability of all materials. Numerous national and international standards and test methods can be implemented with these devices. High reproducibility is guaranteed by measuring and controlling all essential program parameters.
The sunlight simulation chambers SunEvent and SolarClimaticSC600 (Weiss Umwelttechnik GmbH) can be used to test entire components or component groups. The combination of irradiation equipment and climate chamber enables tests to be carried out in a wide temperature range from -30°C to +100°C. Complex cycles with frost and heat phases as well as day and night sections can be realized. Customer-specific test sequences can also be programmed.